Worm gears are ideal for systems that need a bit more power when turning.
If you’ve ever wondered how to select the right gear for your application or why a worm gear might be the best choice for your needs, you’re not alone. Worm gears play a crucial role in various engineering applications.
They offer unique advantages but also come with their own set of challenges.
I will help guide you by breaking down the essentials of worm gears, explaining their components and how they fit into different applications. By the end, you’ll have a clear understanding of worm gears and how they can benefit your projects.
What is worm gear?
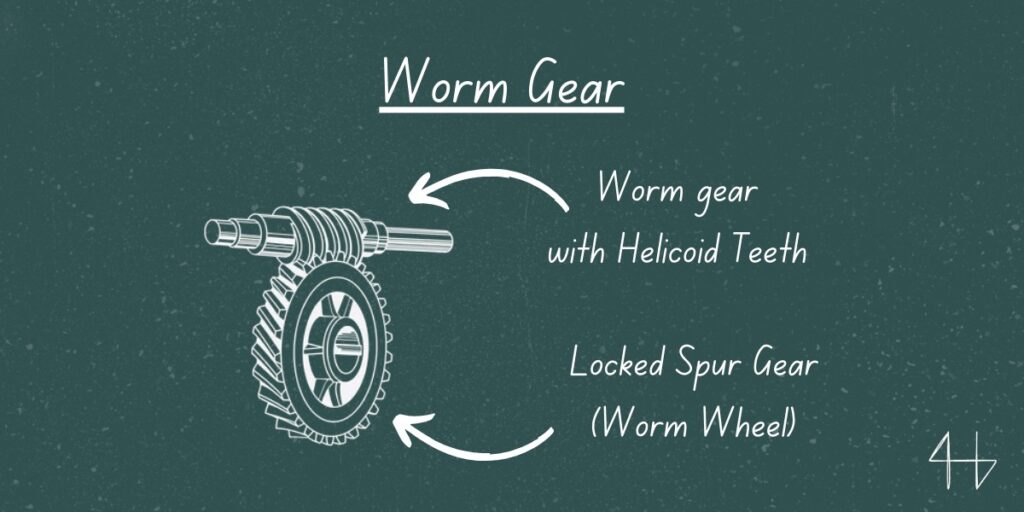
A worm gear is a special type of gear train that consists a screw (called the worm) and a gear wheel (called the worm wheel).
When the worm turns, it moves the worm wheel, which is useful for changing the direction of movement and controlling speed. This setup is great for situations where you need to slow things down a lot while boosting the power, like in car transmissions or winches.
The worm gear set can achieve very high gear ratios, sometimes up to 100:1, meaning you can get a lot of torque with just a little bit of movement.
The Working Principle of Worm Gears
Imagine a worm gear system where the worm (the spiral-shaped gear) rotates and meshes with the worm wheel (the round gear with teeth).
As the worm turns, its spiral thread pushes against the teeth of the worm wheel, making it spin. The gear ratio is determined by comparing the number of teeth on the worm wheel to the number of starts (spirals) on the worm.

For instance, if you have a worm with a single spiral and a 20-tooth wheel, you’ll get a 20:1 reduction ratio. This means the worm needs to spin 20 times for the wheel to make just one full turn.
This setup is useful in many real-life applications where precise, high-ratio speed reduction is needed, like in elevators or heavy machinery.
How to Identify Worm Gears?
A worm gear system consists of a worm and a worm wheel. The worm looks like a screw (screw face pushes) with a spiral thread, and it turns the worm wheel, which has teeth similar to a standard gear.
This setup creates a sliding contact between the worm and the worm wheel.
To spot a worm gear in action, check for an output shaft connected at a right angle to the worm’s rotation axis. This unique arrangement allows worm gears to provide high torque and reduce speed, making them perfect for applications like gearboxes and conveyors.
Worm Gear vs Screw Gears
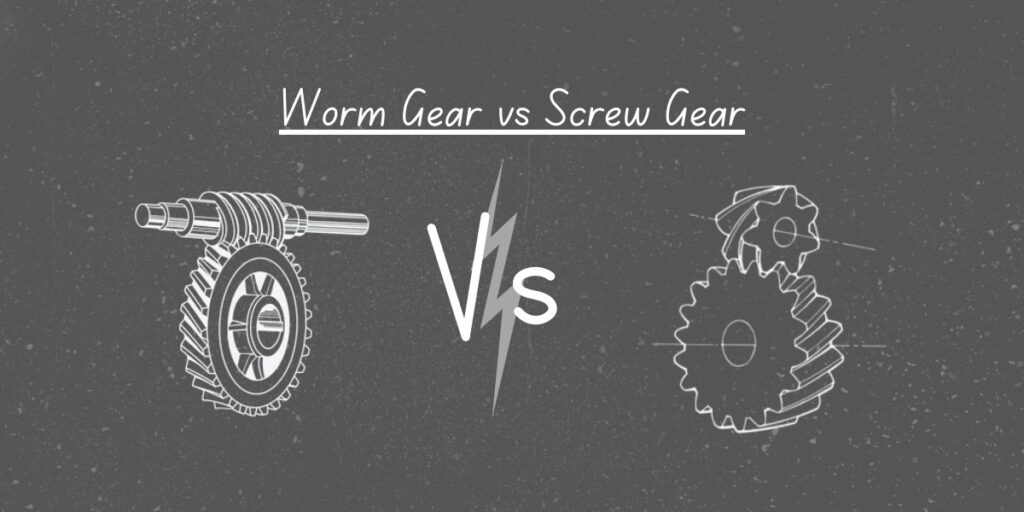
When choosing between worm gears and screw gears (or screw drives), it’s helpful to understand their characteristics.
Worm gears are great for situations where you need to significantly reduce the speed of a rotating shaft while increasing the torque (the turning force).
For example, if you’re working with heavy machinery or a car’s steering system, worm gears are ideal because they provide strong, reliable power transfer with a high reduction ratio.
On the other hand, screw gears are used when you need to convert rotational motion into linear movement, like the lead screws found in 3D printers or CNC machines.
They work well for precise adjustments but usually require multiple stages to achieve high reductions.
So, if your project involves moving something back and forth in a straight line with accuracy, screw gears are your go-to.
Understanding these differences helps you choose the right gear for your specific needs, ensuring your machinery operates smoothly and efficiently.
When to use worm gear
The Primary use of a worm gear is to reduce speed and increase torque. So you would use a worm gear when designing a system where speed is less important than output torque.
For example, in machinery like elevators or conveyor systems, worm gears can slow down the motor’s speed while increasing the force applied to the output shaft.
This is crucial when you need precise control or need to protect your equipment from sudden impacts. By using worm gears, you ensure smooth operation and longevity for your machinery.
How are Worm Gears Manufactured?
Manufacturing worm gears involves several precise steps to ensure they work smoothly and last long.
The worm is usually made from strong steel to handle high forces, while the worm wheel is often made from softer materials like bronze. This choice helps reduce wear and tear over time.
The process includes machining, casting, or forging, and often requires careful cutting and grinding to make sure the worm and wheel fit together perfectly. This precision is crucial because it affects how well the gears perform in real-life applications, such as in machinery or vehicles.
Applications of Worm Gear
Worm gears are used in various real-world applications where precise control and high torque are needed. Let’s explore some common uses.
Lifts / Elevators
In lifts and elevators, worm gears help control the movement of the car smoothly.
They provide a high gear ratio, which makes lifting heavy loads easier and safer. The worm gear’s ability to hold the elevator in place when stationary is crucial for safety.
Tuning Instruments
Worm gears are essential in tuning musical instruments, such as guitars and pianos.
They allow for fine adjustments with minimal backlash (slack) thanks to their high gear ratio. This precision ensures that instruments stay perfectly tuned.
Cranes and Hoists
Cranes and hoists use worm gears to lift heavy objects with precision.
The gears reduce speed but increase torque, making it easier to move large loads. They also help keep the load in place when the crane or hoist is not in operation.
Mining Machinery
In mining machinery, worm gears manage the heavy and continuous loads involved in extraction processes.
They provide high torque and durability, which are essential for moving large amounts of material and handling toughconditions in mines.
Automatic Gates and Conveyors
Worm gears control the movement of automatic gates and conveyors, allowing them to operate smoothly and reliably.
They offer high gear ratios for smooth motion and are good at holding the position, which is important for both gates and conveyor systems.
Advantages and Disadvantages of worm gear
Advantages
Disadvantages
Limitations
Worm gears have their share of limitations that can impact their effectiveness in certain applications.
One major issue is heat generation. The high friction in worm gears creates a lot of heat, which can cause parts to expand and fail, especially under heavy loads or continuous use. This means you might need extra cooling systems or have tolimit how fast or heavy the gear operates.
Another challenge is maintenance. Worm gears require regular lubrication and can wear out quickly, leading to higher maintenance costs and more downtime. This can be a problem in settings where reliability is crucial.
Efficiency is also a concern. Worm gears are not as energy-efficient as other gear types, such as hypoid gears. Inapplications where saving energy is important, like in electric motors, this can be a significant drawback.
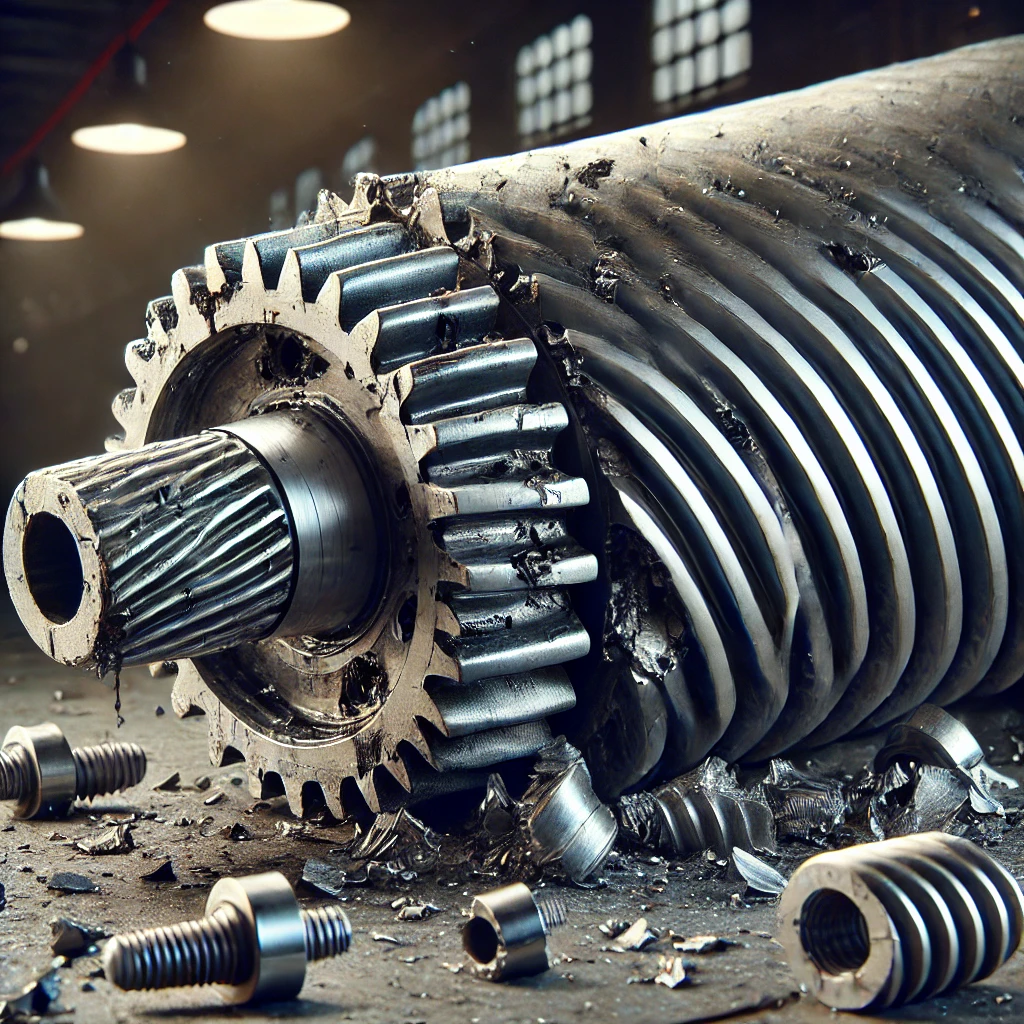
In summary, while worm gears are great for their compact design and high gear ratios, their issues with heat, maintenance, and efficiency need to be considered carefully when designing mechanical systems.
Wrapping up
Worm gears are a type of gear system that consists of a worm (screw) and a worm wheel (gear).
They are known for providing high torque and compact design but can suffer from heat generation, high maintenance needs, and lower efficiency compared toother gears.
These factors should be weighed when considering them for mechanical applications.
FAQs

What is the main advantage of using worm gears?
The main advantage of worm gears is their ability to provide high torque in a compact space. They also offer excellent gear reduction ratios and can operate smoothly in noisy environments.
How are worm gears used in real life?
Worm gears are commonly used in elevators, conveyor systems, and tuning mechanisms for musical instruments. Their high torque and compact design make them ideal for applications requiring precise movement and high reduction ratios.
Are worm gears inefficient?
Yes, worm gears are generally less efficient compared to other gear types due to high friction, which generates heat and results in energy loss. This inefficiency can be a drawback in energy-sensitive applications.